A longstanding customer who we have helped with many projects asked us for advise on a particular problem they were having with filter cake waste. The filter cake was being deposited into a hooklift container from a fixed position. Due to the nature of the waste this was creating a build up in the container – a ‘pyramid effect’. This meant that although the waste was very dense it was not filling correctly and resulted in the container having to be emptied on a much more frequent basis.
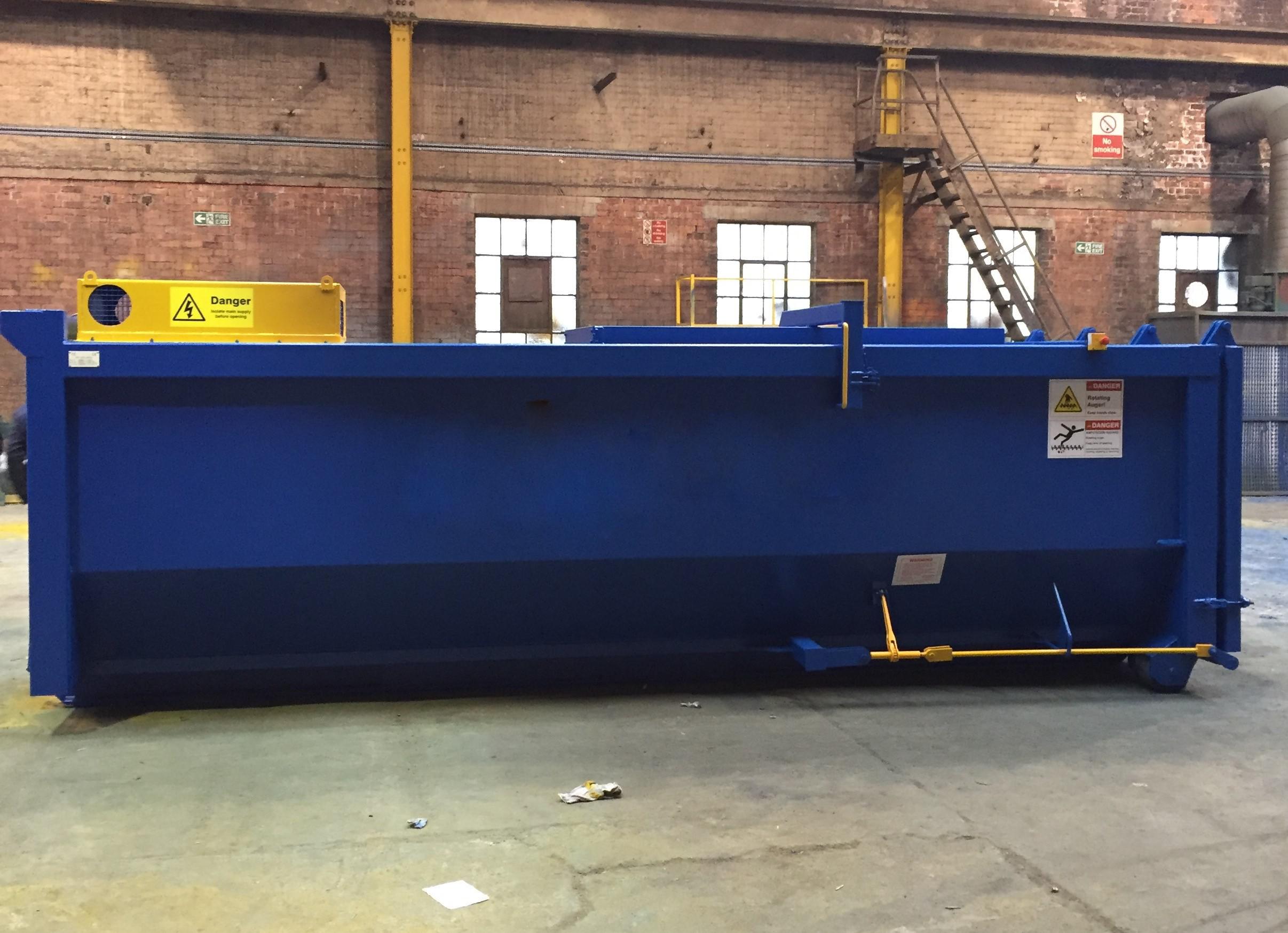
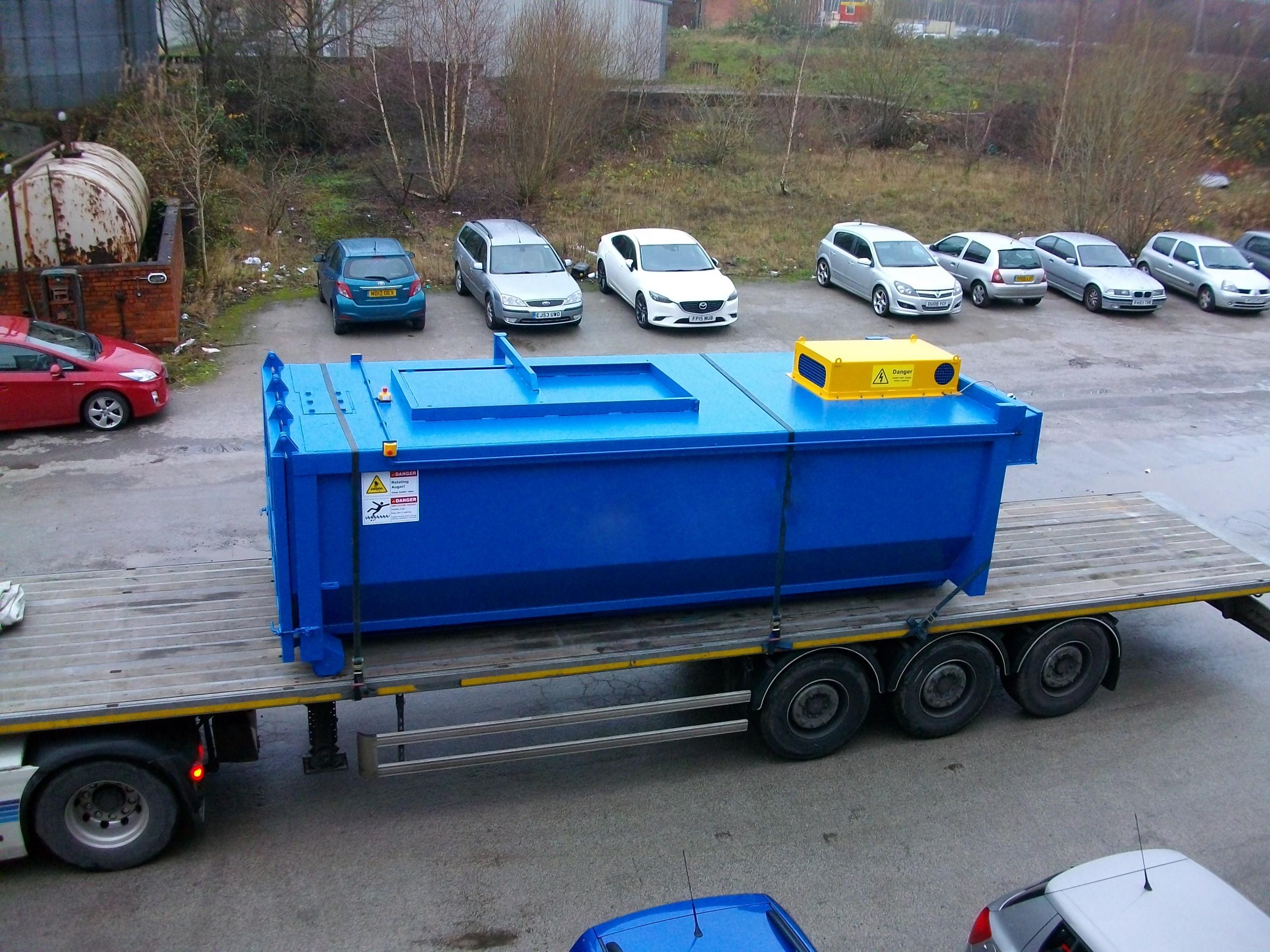
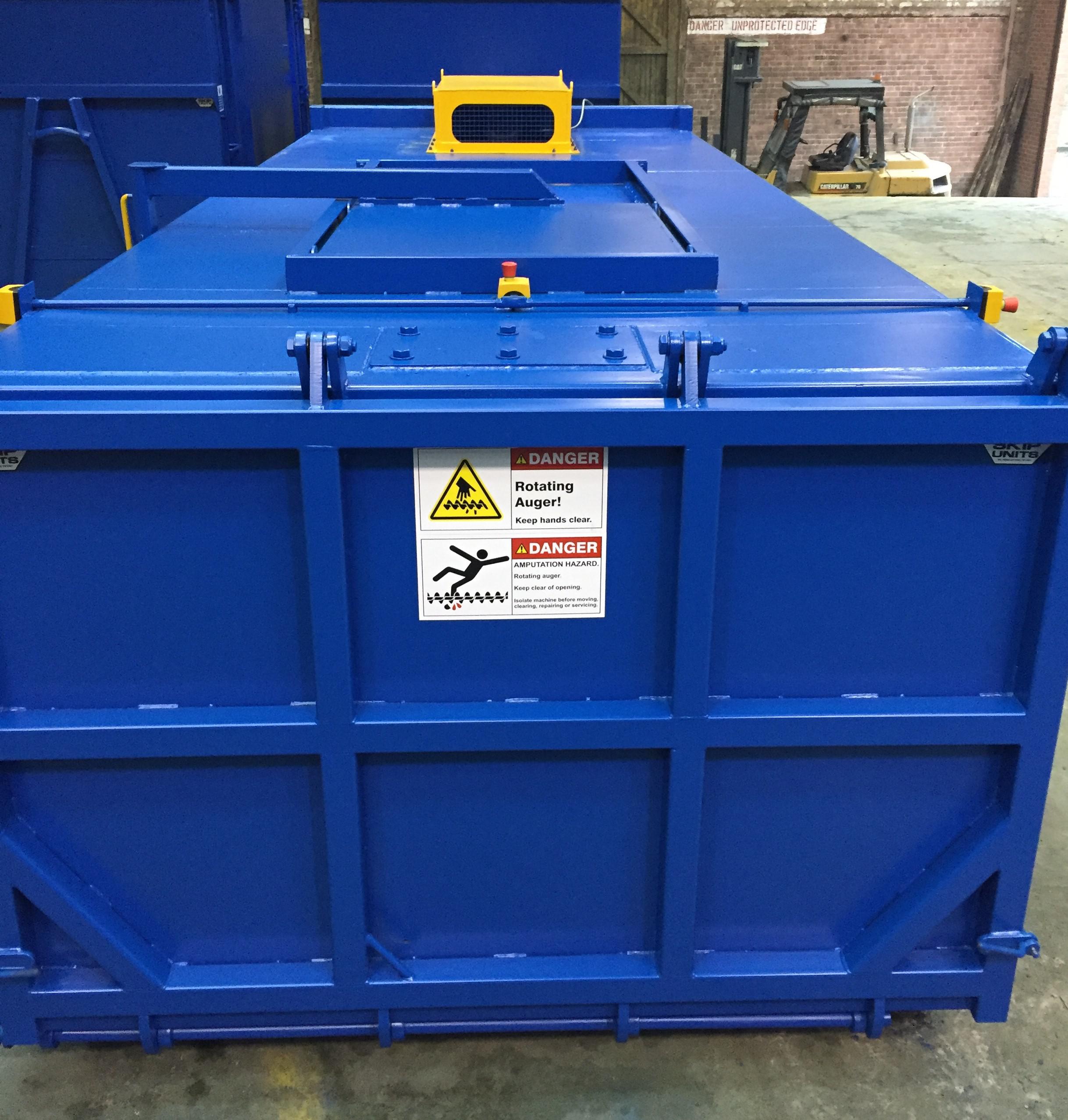
Solving the ‘pyramid effect’ issue
Skip Units proposed the use of an enclosed container with a levelling screw (auger) to help evenly distribute the waste across the length of the container. Some of the engineering factors to overcome were specifying and supporting an auger nearly 5 metres long and selecting the correct drive gear to rotate the screw.
The solution was to supply a 25 cubic yard enclosed container with levelling screw turning at nearly 63RPM, driven by a 5.5kw motor via sprockets and chain. The loading hatch was designed to be opened and closed at ground level on a roller system for ease of movement. This removed any requirement to access the roof of the container, except for maintenance.
The result was a container that was evenly filled and more than halved the exchange frequency providing a substantial saving on transport cost and a quick payback on the investment in the technology.
View our Products